Bulk Material!
Piping construction plays an essential role in the construction of chemical plants: Typically, it is a large and complex part of the project. We spoke with Markus Mook, Head of Construction Materials at thyssenkrupp Uhde GmbH, about what distinguishes materials management in this industry.
» What is so unique about materials management in piping construction? «
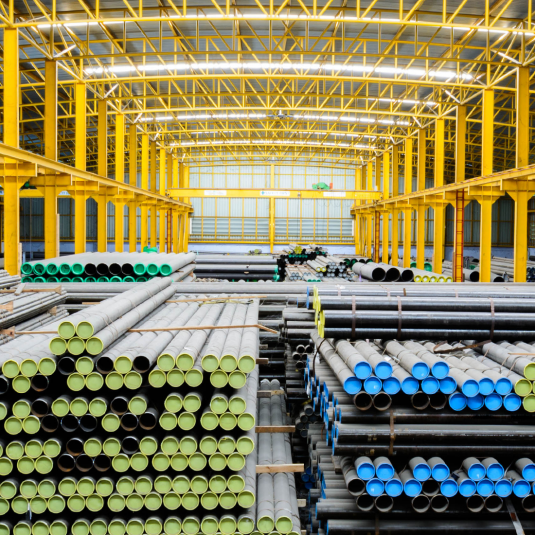
Markus Mook:
Piping construction is not carried out in the same way as the „normal“ installation of a compressor or a machine, etc., of those components that have one particular installation location. In piping construction, you are dealing with so-called bulk material, i.e. components that are always the same (pipes, flanges, fittings, bolts and gaskets, etc.). Bulk material offers x possible installation locations. In a piping system, for example, a certain bend may occur x times in the entire plant. Based on the planning, you genrally know which component has to be installed in which pipe. When the material is delivered, however, it is not yet known exactly where a particular individual bend will be fitted in the end…
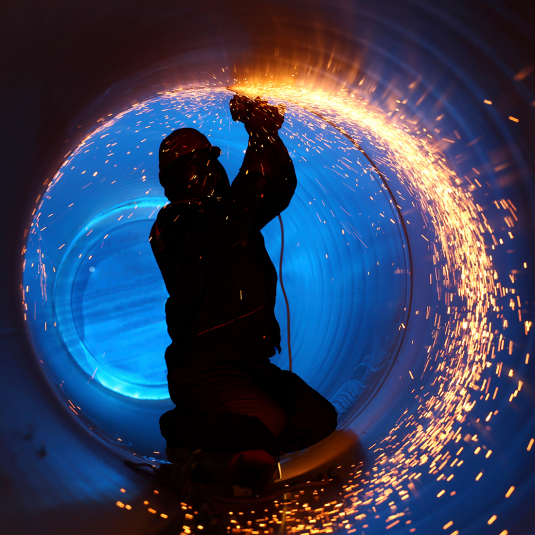
Another characteristic of piping construction is prefabrication: Pipe components are welded together in advance to form larger units (so-called spools), i.e. flanges, pipe bends, etc. are pre-assembled. This is done either on site or off site. On site, larger and more complex partial prefabrications are possible.
Away from the construction site, prefabricated pipe parts must remain available in transportable units, as they have to fit into containers or trucks. Material is always delivered over an extended period of time. When you start prefabrication, you often don‘t have your warehouses completely filled. You have to be able to react to all of that.
» In your experience, what does software for piping construction have to acomplish? «
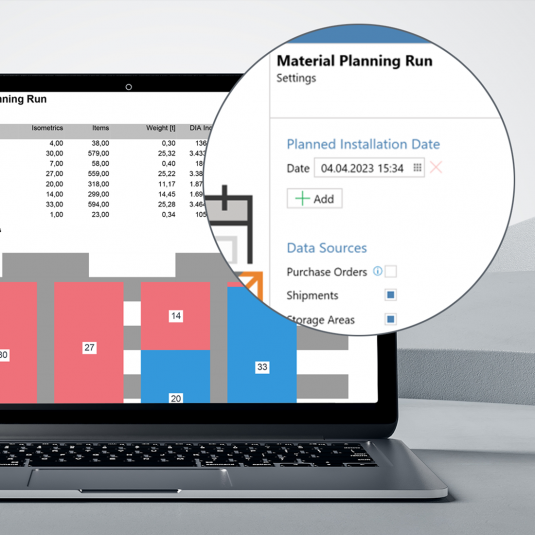
The solution must help us avoid material bottlenecks and downtimes. It must be possible to control the material flow so that there is always enough materials on site to utilize the calculated trades to capacity. Specifically, the software must answer:
- What can be built with the current stock or with the material that is already in the supply?
- What is in the supply? If there are larger quantities in the supply, how many employees does a subcontractor have to mobilize to ensure that this can be handled?
For us, the buildability analyses that we do with Insite LMS are absolutely helpful for this. They allow us to determine in advance for specific installation days and pipe systems whether the required bulk material will be available and to reserve all the parts necessary right away.
About Markus Mook
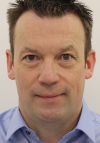
As Head of Construction Materials at thyssenkrupp Uhde GmbH, Markus Mook has been responsible for materials management on construction sites for almost 20 years. He studied mechanical engineering and is the father of two children.
We thank Markus Mook for the interview and the successful cooperation.